Meet SprutCAM X
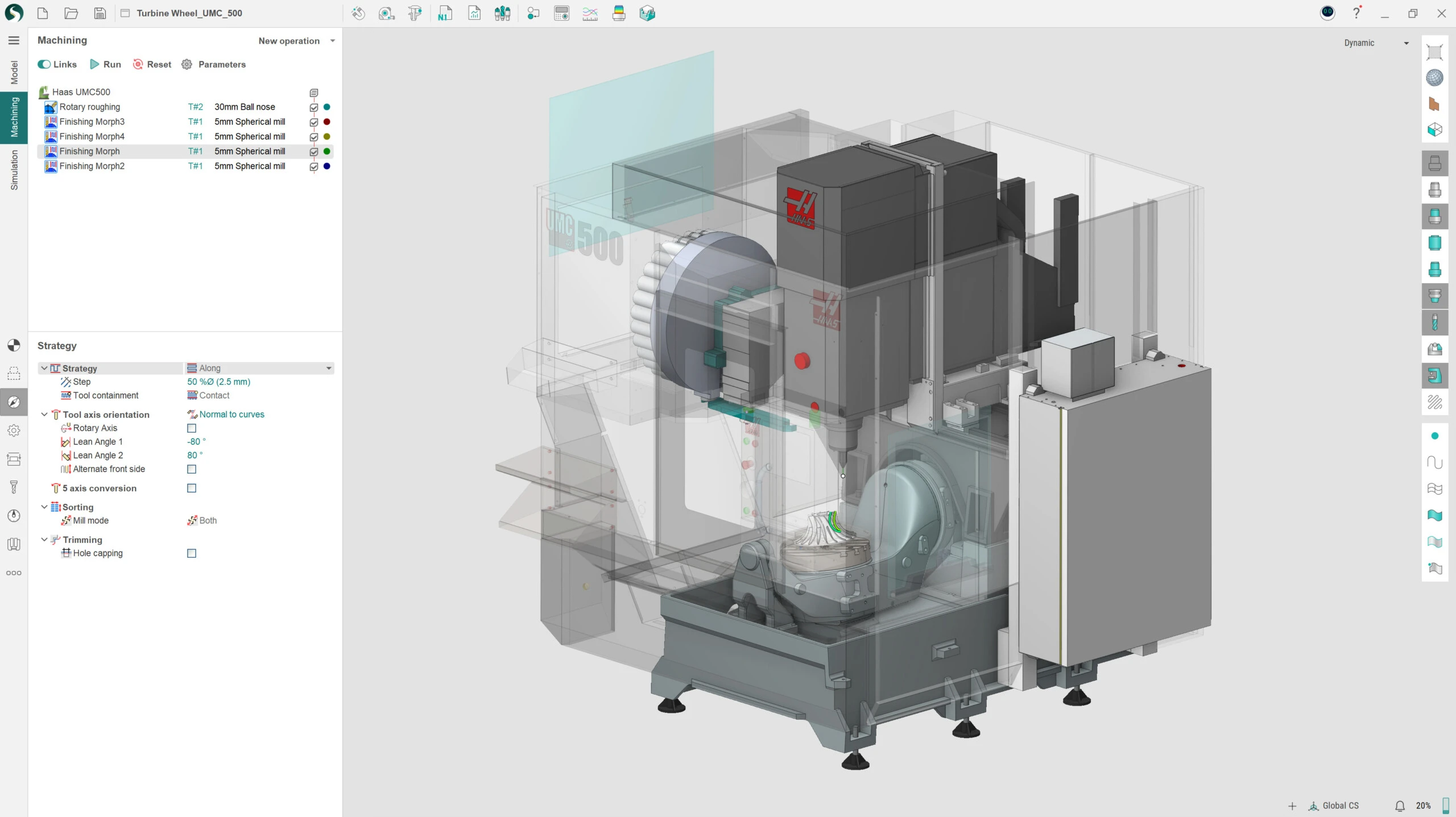
Machine-aware CAD/CAM platform
SprutCAM X introduced the Machine-Aware programming approach back in 2001, establishing it as the high-end foundation for a CAM software. This innovative approach involves considering machine limitations during the initial toolpath calculation, setting it apart from traditional CAM methods that operate in abstract space before converting to real machine code during simulation or postprocessing.
As machine kinematics become increasingly complex, the benefits of the Machine-Aware approach continue to grow. This advanced CAD/CAM software not only ensures appropriate safety for programming 5-axis and mill-turn machines but also provides a foundation for a transparent and intuitive user experience.
Your CNC Machine digital twin
The MachineMaker app allows you to generate a digital replica of your CNC machine in a matter of minutes. This digital twin is intended for use in programming the CNC machine within the CAD/CAM software SprutCAM X.
Furthermore, MachineMaker features an extensive library of readily available individual components, as well as complete pre-designed digital twins of CNC machines and postprocessors.
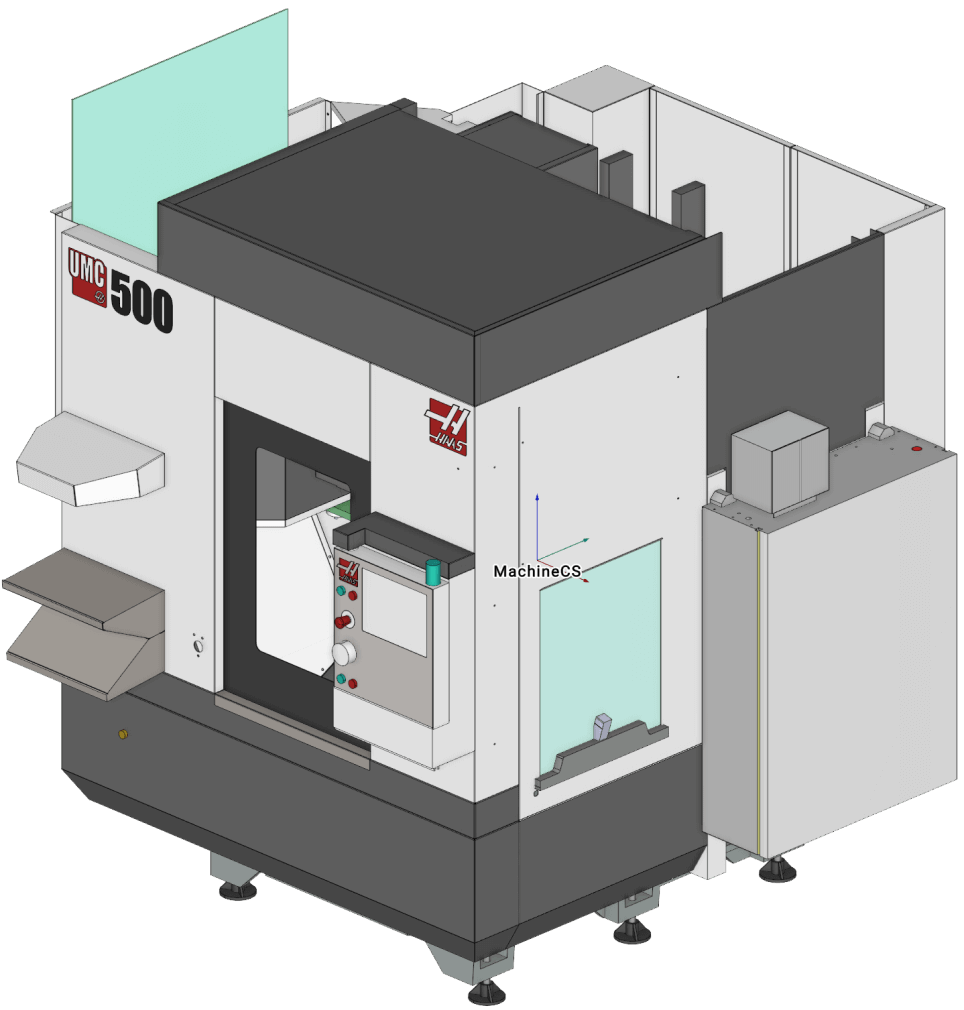
Product Highlights
Applications
Technology highlight:
Adaptive SC
This high-speed machining cycle is specifically designed for roughing to substantially decrease cycle times and extend tool life. Its technology automatically regulates chip loads and lateral cutting forces while maintaining the cutter engagement angle and machine axes acceleration within optimal ranges.
With Adaptive SC, the machine can make deeper cuts at higher feedrates, which are also automatically optimized throughout the toolpath for maximum efficiency. In comparison to traditional machining methods, Adaptive SC provides the following benefits:
70%
reduction in cycle time
500%
increase in tool life
Applications
Technology highlight:
Adaptive SC
This high-speed machining cycle is specifically designed for roughing to substantially decrease cycle times and extend tool life. Its technology automatically regulates chip loads and lateral cutting forces while maintaining the cutter engagement angle and machine axes acceleration within optimal ranges.
With Adaptive SC, the machine can make deeper cuts at higher feedrates, which are also automatically optimized throughout the toolpath for maximum efficiency. In comparison to traditional machining methods, Adaptive SC provides the following benefits:
70%
reduction in cycle time
500%
increase in tool life