Getting accuracy when programming robots
June 29, 2020
We need your opinion: solution for achieving required accuracy when programming robots
Disclaimer
We at SprutCAM are making research to understand market demand of the solution for achieving better accuracy for robots. Most customers face accuracy problem when implementing their robot cells. We have an idea how we can solve it.
Besides accuracy there is another obstacle for the new SprutCAM X Robots users — tool and base calibration. Here on this page we also offer automatic tool and base calibration solution idea for eliminating inaccuracy and make it user-friendly.
If getting required accuracy is a relevant problem for you please read this document and submit a poll after that.
Problem description
Getting required accuracy when programming robot is challenge.
Main reasons of poor accuracy:
- Manual not precise tool and base calibration;
- Robot absolute positioning accuracy: >0.7 mm (up to 3mm in real life).
This results in:
- Large robot idle periods for readjustment when changing the program and the part to be machined;
- High rejection rate;
- Inability to fulfill customers requirements concerning machining accuracy.
But:
Robot pose repeatability: 0.05mm
Higher accuracy for pose repeatability makes it possible to achieve better accuracy for absolute pose with precise tool, base and job zone calibration routines.
Solution
Fully integrated turn-key solution for robot programming in SprutCAM featuring automatic tool and base calibration and compensation of robot absolute pose inaccuracy throughout all job zone.
Automatic tool and base calibration
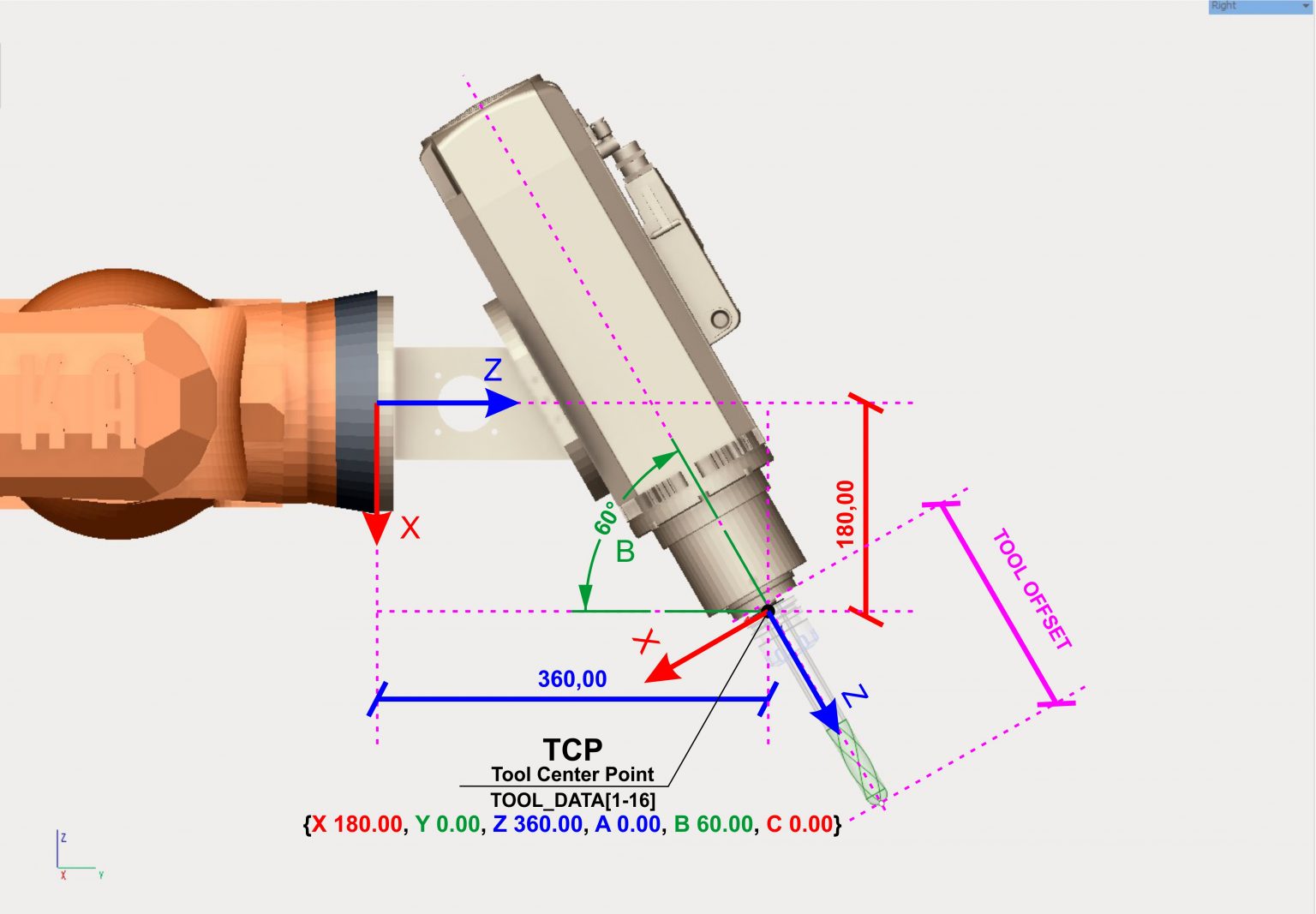
Software + hardware solution which includes industrial vision, which features:
- High precision calibration, especially comparing to manual calibration;
- Fully automatic tool and base calibration;
- Automatic tool and base calibration data transfer into SprutCAM X;
- Eliminate random errors caused by human factor;
- Less robot idle periods for readjustment.
Solution will consist of
- Standalone application for robot direct routing and getting feedback;
- Industrial vision system. Different price options available for different accuracy requirements.
- Software module inside SprutCAM for automatic calibration data transfer to SprutCAM X;
Robot job zone calibration
High end solution for getting high absolute positioning accuracy throughout all across robot job zone.
Faro, Creaform or other high-end industrial vision usage required.
Getting: 0.5…0.2 mm absolute accuracy across job zone.
Hot it works:
- After robot cell installation a special software application generates evenly distributed point cloud inside of the job zone and robot program for sequentially arrive to all these points;
- After robot arrives to every point the industrial vision measures real position of the robot;
- After this procedure is finished we get the matrix containing offsets between ideal and real coordinates inside the job zone. Let’s name it Job Zone Calibration Matrix;
- After robot program post-processing a special procedure is executed. It adjusts coordinates in the program using Job Zone Calibration Matrix and special interpolation algorithm to compensate robot absolute positioning inaccuracy.
Software part of the solution consists of two modules:
- Standalone application for robot routing and getting Job Zone Calibration Matrix;
- SprutCAM add-on which takes Job Zone Calibration Matrix as an input data and includes robot program recalculation algorithm.
End user has to perform that job zone calibration once. After that it is enough to use Job Zone Calibration Matrix for robot program adjustment to achieve accuracy. End user will have to re-calibrate robot job zone as robot cell mechanisms get worn.
Robot job zone calibration is a procedure performed by robot system integrator.
Calibration process example
Calibration results example
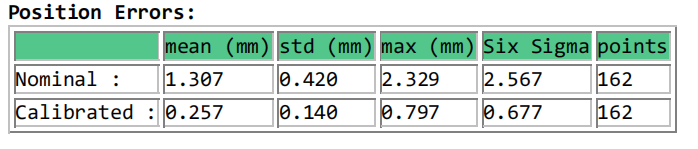
Robot programming workflow for achieving better accuracy
Tool and base calibration
- Put a part into job zone;
- Install a tool;
- Run SprutCAM with robot cell model and import the part model;
- Run SprutCAM add-on for automated tool and base calibration:
- Users sets several parameters for tool and base calibration;
- Tool calibration app will generate collision-free toolpath for precise tool calibration
- Tool calibration app sends control program directly into robot controller
- Robot runs the program;
- Industrial vision camera captures required data during program execution;
- Necessary calculations are performed and tool calibration data is imported into SprutCAM X project.
- Same procedure is performed for base calibration.
- User created all necessary operations in SprutCAM, makes post-processing and runs the program on robot. Also existing project can be loaded and user just recalculates the toolpath after tool and base are calibrated.
Adjusting control program with Job Zone Calibration Matrix
- Create and postprocess SprutCAM project as usual;
- Run a special add-on for final control program adjustment for compensation of robot pose inaccuracy;
- If desired it is possible to run the simulation of calibrated control program in SprutCAM X before execution on a real robot;
- Transfer the program to robot and run.
Interested in a solution for getting high accuracy with robots?
We need to find out critical details to better understand the form to this solution.
Please submit this form, we will get in touch with you.
Error: Contact form not found.
Error: Contact form not found.
id="27242" title="Get a quote"]