3D Horse made with SprutCAM X
Mei 27, 2024
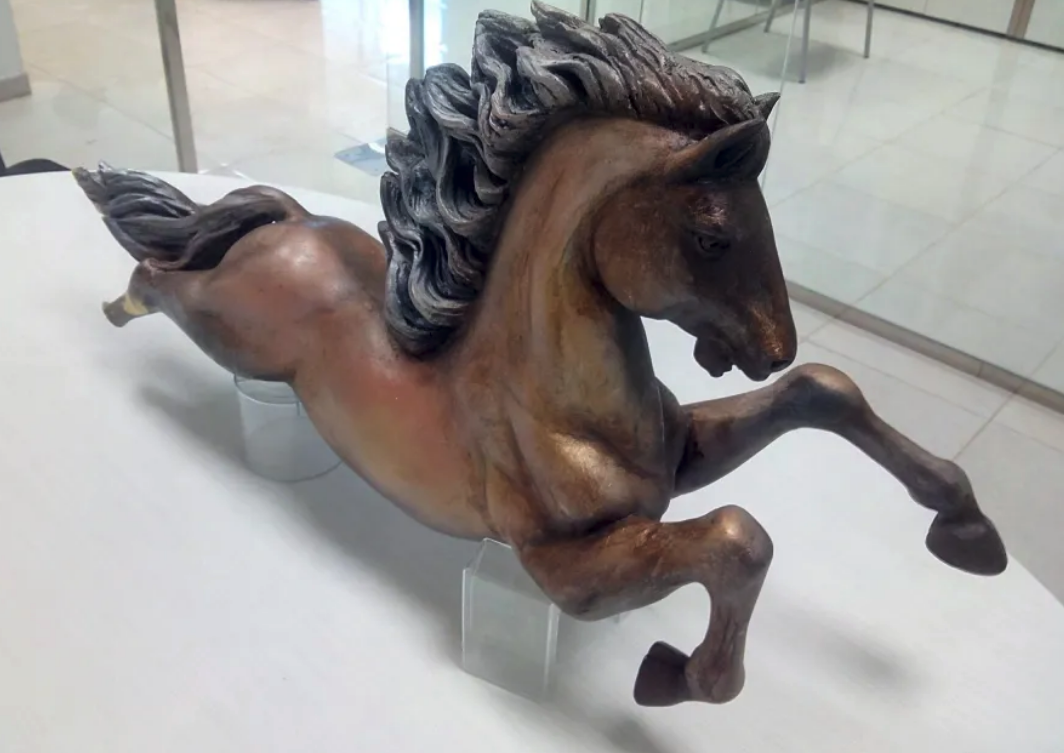
Sculpture is one of the oldest forms of three-dimensional visual art. During a sculpting process, artists utilise a variety of techniques and employ different tools to reform a piece of clay until it satisfies the intent of their artistic expression. In the contemporary industrialised context, computer numerical control (CNC) milling is a widely used manufacturing technique for three-dimensional sculptural artefacts. It often substitutes traditional processes, including stone carving and foam cutting. However, conventional CNC milling techniques are limited when applied to soft materials. It is well-known that highly ductile materials are notoriously difficult to cut mechanically.
Human sculpting still holds a special place due to its close association with arts and crafts. Due to the non-linear nature of the design process, artists usually rely on an interactive process to think and create through minds and hands simultaneously. The often imperfect surface finish records the working process of the artist and thus becomes a feature of artistic expression. Such patterns and textures are difficult to achieve and often not considered in CNC machining, and if required, they are typically only achieved by subsequent special surface treatments. Robotic sculpting automates the sculpting process by generating feasible motion trajectories that can be executed by robot arms.
Over the past decade, there has been a significant advancement in robotic fabrication, particularly in the field of architecture. The democratisation of computer-aided design (CAD) to computer-aided manufacturing (CAM) tools has led to novel inquiries into the potential of industrial robotic arms in mass customisation workflows and their role as a versatile fabrication tool. This renewed interest has led to a surge in research in the field, facilitated by the proliferation of dedicated robotic fabrication facilities in architecture schools worldwide.
Robotic milling is a process whereby material is cut from a mould in order to sculpt a specific or complex shape. The material can be any type, including plastic, metal, foam, wood or alloys. Milling robots are capable of making the exact cuts and the precise movements necessary to produce the highest quality parts. The process is generally divided into two stages. The first stage is the rapid and cost-effective removal of material, while the second stage is the finishing of the structure based on dimensions, degree of surface, furrows, profiles, openings and even three-dimensional surface contours.
Automated robot machining systems are flexible and versatile tools designed to address the removal of specific material. Milling robots generally perform a routine following PTP movements (point to point) or a linear or curved group in 3D programming. This process is repeated throughout the life cycle, providing a large workspace. This robotic solution is one of the most profitable and considerably more flexible. The robot milling work cells are designed to have multi-part accessories.
For example MecData uses robotic sculpting in fabrication process for the sculpture of a 4.5 metre long horse from a 40cm gloss painted resin figure.
Scanned in 2 positions to have the whole piece captured, with Calibry Nest we have joined both scans into one piece giving the complete final result. Using CAD/CAM technology and milling machines, the replica will be made from this 3D. Capturing the textures will allow a more detailed and accurate copy of the surface finish to be made.
Once the part has been scanned and the mesh has been obtained, it has been divided into different parts so that it can be milled more easily. Thanks to SprutCAM, both in its version for robots and for large milling machines, the milling paths necessary for the manufacture of each component are created. The programs generated in SprutCAM are passed to the corresponding machines and the parts are assembled until the final product is obtained.