Custom handlebar yokes for Harley Davidson motorbikes
Juni 3, 2024
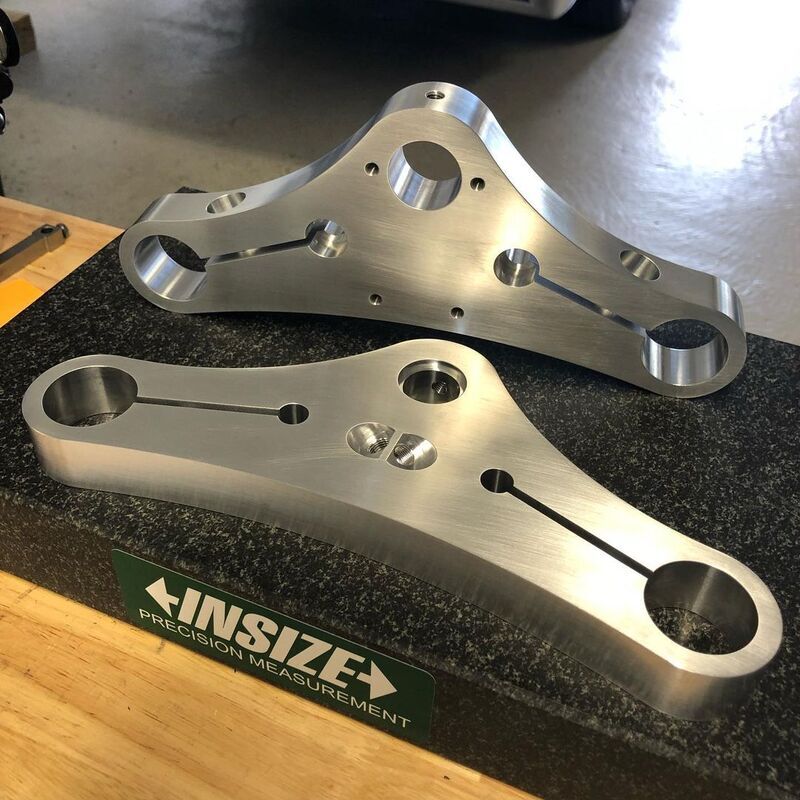
SprutCAM X system is the ultimate solution for crafting bespoke components for automobiles and motorcycles. One prime illustration of its capabilities comes from Solo Precision Ltd, a valued UK customer. They recently tackled the task of replicating handlebar yokes for a custom Harley Davidson, reverse engineering them from vintage custom parts. The intricate yolks were meticulously milled from high-quality aluminum using a Hurco CNC machine, a process made possible by SprutCAM X.
In the words of the satisfied customer, “I couldn’t do it without SprutCAM; it’s an excellent system.”
This accomplishment underscores the invaluable role of SprutCAM X in the world of precision engineering for automotive customization.
What operations SprutCAM X employed for making this part:
1) Roughing waterline
The waterline roughing operation is used for preliminary rough machining of models of a complex shape, which have significant differences to the workpiece.
2) Face milling
The face milling operation removes stock on a given horizontal plane with one of the following strategies:
a) One pass,
b) One way,
c) Zigzag,
d) Optimized zigzag
e) Spiral.
3) 2D contour
The operation is designed for machining along horizontal contours or curve projections on the horizontal plane, cylinder or figure of revolution. It is also possible machining with the cylindrical and polar interpolation.
4) Holes machining
The hole machining operations are designed for drilling, centering, boring, countersinking, tapping, thread milling and hole pocketing. It can machine holes that are not lying in the same plane and that are not lying in orthogonal planes. The operation can be used both for the machining of holes in a model, or for pre-drilling of the tool plunge points for the pocketing and waterline roughingwaterline roughing operations.
SprutCAM X for the automotive industry
SprutCAM X is a powerful CAM software that is commonly used in the automotive industry for programming CNC machines to manufacture various components and parts. Here are some specific ways in which SprutCAM X is used in the automotive industry:
1. Toolpath generation: SprutCAM X allows users to create toolpaths for machining operations such as milling, turning, and drilling. This is essential for manufacturing automotive components with high precision and accuracy.
2. Multi-axis machining: SprutCAM X supports multi-axis machining, which is often required for complex automotive parts that have intricate geometries. This capability allows manufacturers to produce parts with greater efficiency and quality.
3. Simulation: SprutCAM X includes advanced simulation features that enable users to visualize the machining process before actually cutting the material. This helps to identify potential issues and optimize the machining process to reduce errors and improve overall efficiency.
4. Post-processing: SprutCAM X offers post-processing capabilities that allow users to generate machine-specific G-code for CNC machines. This ensures seamless communication between the CAM software and the CNC machine, resulting in accurate and reliable machining operations.
Overall, SprutCAM X is a versatile CAM software that plays a crucial role in the automotive industry by enabling manufacturers to streamline their production processes, increase productivity, and produce high-quality automotive components.
What operations SprutCAM X employed for making this part:
1) Roughing waterline The waterline roughing operation is used for preliminary rough machining of models of a complex shape, which have significant differences to the workpiece.
2) Face milling The face milling operation removes stock on a given horizontal plane with one of the following strategies: a) One pass, b) One way, c) Zigzag, d) Optimized zigzag, e) Spiral.
3) 2D contour The operation is designed for machining along horizontal contours or curve projections on the horizontal plane, cylinder or figure of revolution. It is also possible machining with the cylindrical and polar interpolation.
4) Holes machining The hole machining operations are designed for drilling, centering, boring, countersinking, tapping, thread milling and hole pocketing. It can machine holes that are not lying in the same plane and that are not lying in orthogonal planes. The operation can be used both for the machining of holes in a model, or for pre-drilling of the tool plunge points for the pocketing and waterline roughingwaterline roughing operations.
SprutCAM X for the automotive industry
SprutCAM X is a powerful CAM software that is commonly used in the automotive industry for programming CNC machines to manufacture various components and parts.
Here are some specific ways in which SprutCAM X is used in the automotive industry:
1. Toolpath generation: SprutCAM X allows users to create toolpaths for machining operations such as milling, turning, and drilling. This is essential for manufacturing automotive components with high precision and accuracy.
2. Multi-axis machining: SprutCAM X supports multi-axis machining, which is often required for complex automotive parts that have intricate geometries. This capability allows manufacturers to produce parts with greater efficiency and quality.
3. Simulation: SprutCAM X includes advanced simulation features that enable users to visualize the machining process before actually cutting the material. This helps to identify potential issues and optimize the machining process to reduce errors and improve overall efficiency.
4. Post-processing: SprutCAM X offers post-processing capabilities that allow users to generate machine-specific G-code for CNC machines. This ensures seamless communication between the CAM software and the CNC machine, resulting in accurate and reliable machining operations. Overall, SprutCAM X is a versatile CAM software that plays a crucial role in the automotive industry by enabling manufacturers to streamline their production processes, increase productivity, and produce high-quality automotive components.