Robot milling art
Ocak 13, 2023
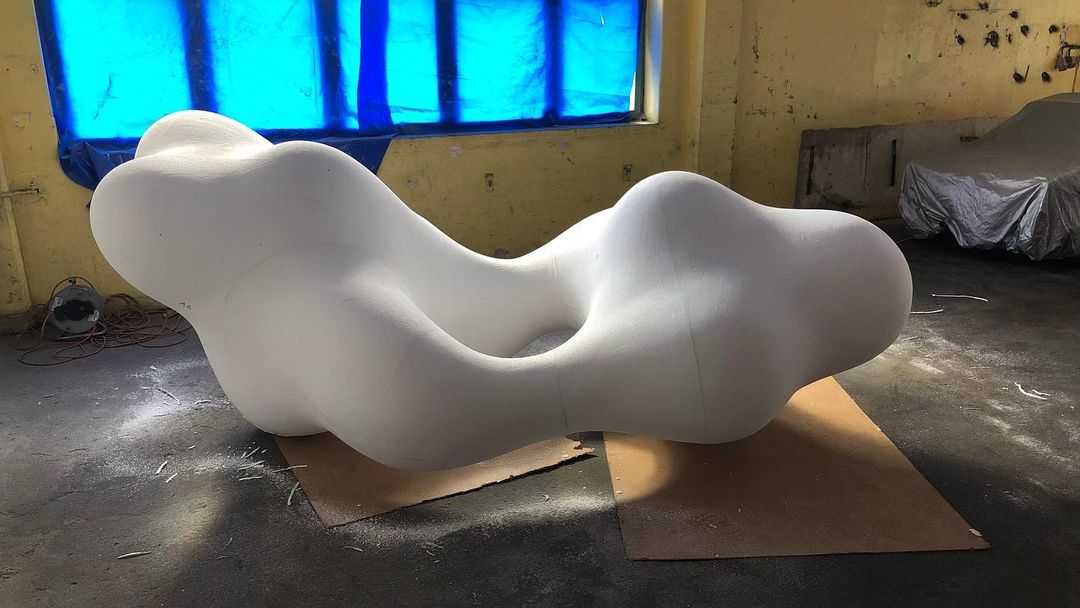
⠀
Det är mycket planering och ritande innan det finns en strategi. Formen måste delas i hanterbara stycken och även vara möjlig att montera ihop igen. Ett stort antal friformsytor modelleras upp i rymden omkring varje form för att trådskära stora volymer 5-axligt innan finfräsning. Och så alla koordinatsystem förstås, inklusive fixeringspunkter som är dolda efter limning. Se sista videon för en kort behind-the-scenes och följ Eva och Storverkstan för att se hur arbetet fortskrider!
⠀
Last summer I was milling a model for a public commission that Eva Hild ( @evahildart ) is now continuing together with @storverkstan. The original object is a small plaster model that was scanned and enlarged to a fairly challenging piece in terms of manufacturing. No flat surfaces, no natural seams and shapes with neither beginning nor end means it’s easy to get lost…
⠀
There’s a lot of planning and drawing before a strategy is set. The model needs to be split into manageable pieces and still be possible to reassemble. A large amount of freeform surfaces are modeled around each shape in order to control 5-axis hot wire cutting of the big volumes before the finishing milling. And all the coordinate systems of course, including connections and fixture points that are hidden in the final assembly. See the last video for a small behind-the-scenes view and follow Eva and Storverkstan to see how it all turns out!”