Understanding the Fundamentals of M-Codes: A Beginner’s Guide to CNC Programming
जनवरी 20, 2023
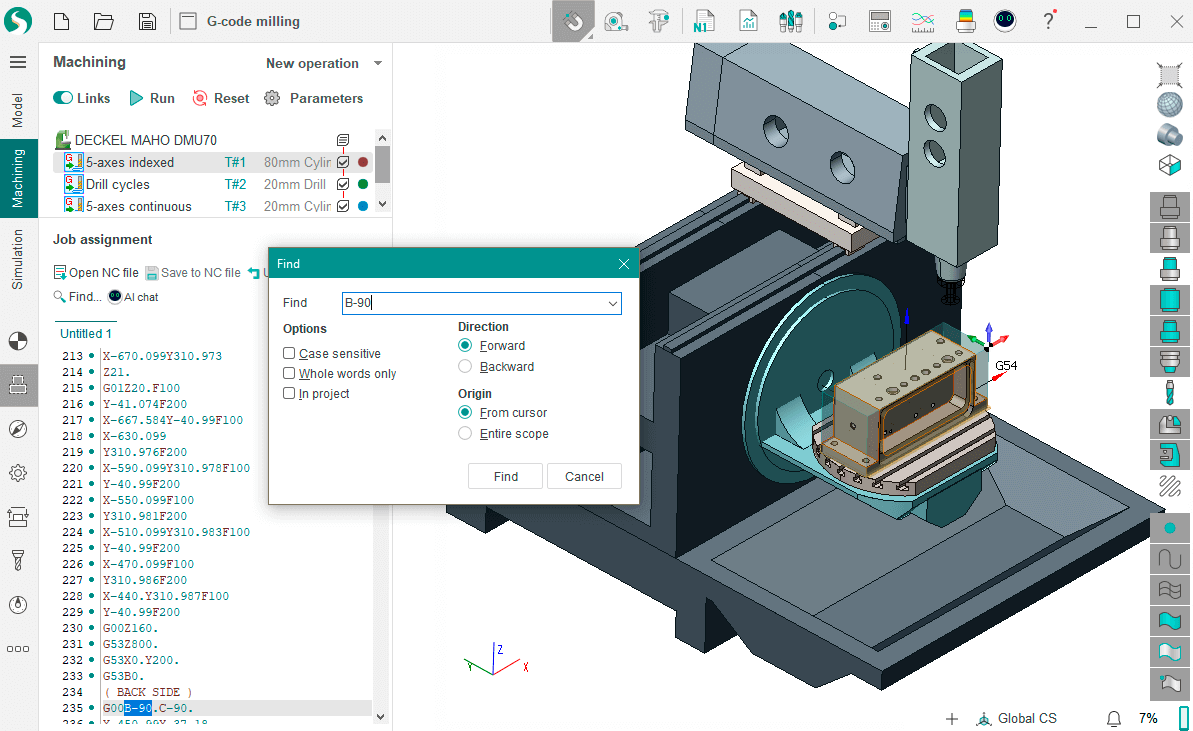
M-codes, also known as miscellaneous function codes, are a type of code used in CNC (computer numerical control) programming to control non-movement related functions on the machine. They are used in conjunction with G-codes, which are used to control the movement of the machine, to create a complete CNC program.
The most basic M-codes include:
- M00: Program stop
- M01: Optional program stop
- M02: End of program
- M03: Spindle on (clockwise)
- M04: Spindle on (counterclockwise)
- M05: Spindle stop
- M06: Tool change
- M08: Coolant on
- M09: Coolant off
- M30: End of program (same as M02)
M-codes are used to control a wide range of functions on a CNC machine, such as spindle speed, coolant flow, and tool changes. The specific functions controlled by M-codes can vary depending on the machine and the specific M-code being used. For example, M03 and M04 are used to turn the spindle on in a clockwise or counterclockwise direction, respectively, while M08 and M09 are used to turn the coolant on or off.
M-codes are also used to control the flow of the program, such as stopping the program (M00 or M01) or ending the program (M02 or M30). These codes provide the machine with the necessary instructions to complete the task and stop the operation when it is done.
It’s also important to note that some M-codes may not be supported by all machines, and some machines may have additional M-codes that are not listed here. Always refer to the specific machine’s manual or documentation for a complete list of supported M-codes.
In conclusion, M-codes are an essential part of CNC programming and are used to control a wide range of non-movement related functions on the machine. Understanding the basic M-codes and their functions can help you to create more efficient and accurate CNC programs and ensure that your machine runs smoothly.
Why you need a CAD/CAM software for CNC machine programming
A CAM (computer-aided manufacturing) software is an essential tool for programming CNC machines. It allows the user to create a program by generating G-code from a 3D model or drawing, rather than manually writing the code. This makes the programming process more efficient and user-friendly, as the user can visually see how the machine will move and make adjustments as needed. Additionally, many CAM software programs include advanced features such as toolpath optimization, collision detection, and post-processing, which can help to improve the quality and accuracy of the finished product. In short, a CAM software makes the process of programming CNC machines much more efficient and precise, allowing for more complex and intricate designs to be produced with a high degree of automation.